[Editor’s note: This article runs in a new section of The Tyee called ‘What Works: The Business of a Healthy Bioregion,’ where you’ll find profiles of people creating the low-carbon, sustainable economy we need from Alaska to California. Find out more about this project and its funders.]
When Mikhail Moore walks down one of the beautiful beaches near his B.C. home, he’s bothered when he sees yet another medical mask — that ubiquitous artifact of the COVID era — lying in the sand. He just hopes it’s not one made by his company.
He can take solace knowing his firm leads not only in manufacturing plastic medical masks by the millions but in developing the complex process of recycling them.
Moore is president of Vitacore Industries Inc., which, in collaboration with a team of researchers at McMaster University, in August 2020 became the first medical mask producer in Canada to make a respirator with Health Canada’s seal of approval.
Today the Port Coquitlam, B.C.-based company produces eight different mask varieties, including the CAN95 and CAN99 types they developed in-house — the best available for preventing COVID transmission.
But almost as soon as they were developed, Vitacore president Moore recognized an issue with the masks: they were yet another source of single-use plastic waste.
“From the very beginning it was on all of our consciousness that we were producing millions of respirators,” said Moore, adding the masks are made from polypropylene, also known as plastic No. 5.
Federal and provincial governments had discussed banning single-use plastics, many of which are made from polypropylene, but no legislation was yet in effect.
“If we’re lucky they’re going to end up in a landfill,” Moore said. “We’ve all seen streets and sidewalks littered with them, or beaches. For me one of the biggest fears was walking the beach and seeing one of ours, a Vitacore respirator, on a beach and just knowing that we had contributed to that pollution.”
B.C. has a better plastic recycling track record than most regions, with 98 per cent of plastics put in blue bins actually being recycled as of 2022.
“It varies a lot depending on where the geography is, because the recycling industry is pretty local,” said Margaret J. Sobkowicz Kline, a plastics engineering professor at the University of Massachusetts Lowell.
In most places in Canada and the United States, Sobkowicz Kline said, “a good fraction” of polyethylene terephthalate and high-density polyethylene, otherwise known as plastics No. 1 and No. 2, are recycled.
“Polypropylene is poised to become the next plastic that’s recycled at a much higher rate,” she said.
But so far Recycle BC doesn’t recycle polypropylene masks, and with the need to separate millions of metal nose pieces and elastic loops from the mask bodies, no one in the province was prepared to recycle them in 2020.
Vitacore saw another gap it could fill.
“Canada is actually the third-largest user of single-use plastics, per capita, in health care out of all of the world. As we’ve increased mask and respirator use, what’s been thrown out has reached astronomical levels,” Moore said.
Working again with researchers at McMaster University, this time with the addition of researchers from the University of British Columbia, Vitacore began investigating options for separating the different recyclable mask materials — metal nose pieces, plastic material, elastic straps — at a volume high and fast enough to be financially worth it.
In early 2021, Planet Impact, the Vitacore Industries Inc. recycling program for hard-to-recycle plastics, was born.
From ‘fluff’ to ‘noodles’ to pellets
The new machines, funded in part with a $900,000 grant from the province, and designed specifically to separate metal soft plastics like polypropylene, were off limits for Tyee photos, as the patent is still pending.
But we did get a look at them and an explanation of how the recycling process works when we visited the company’s Port Coquitlam location in late January.
The new recycling setup, which also works for medical-grade polypropylene gowns, medical nitrile gloves and reusable shopping bags, begins on a conveyor belt that feeds the materials into a shredder, which is surrounded by plastic tarps hanging from a ceiling air filtration system to reduce the airborne “fluff” it creates.
“We have three layers of air extraction in here, just to make sure we don’t have fluff everywhere,” Moore said. Polypropylene fluff isn’t dangerous, he added, but other plastics that could end up in the mix pose a possible fire hazard if not removed.
From there the shredded materials are fed into the extractor, which uses a rotating electromagnet to create an eddy current, which temporarily magnetizes the aluminium nose pieces, causing them to “pop up” into a separate collection container.
From there the plastic is fed through another separation process to filter out non-polypropylene plastics, like the nitrile used to make medical gloves.
The filtered plastic travels down another conveyor belt to the extruder, which heats up the material to its melting point. The molten plastic is filtered again to sift out any non-polypropylene plastics, and the resulting material is pushed out into long “noodle” shapes — kind of like a glue gun working in reverse.
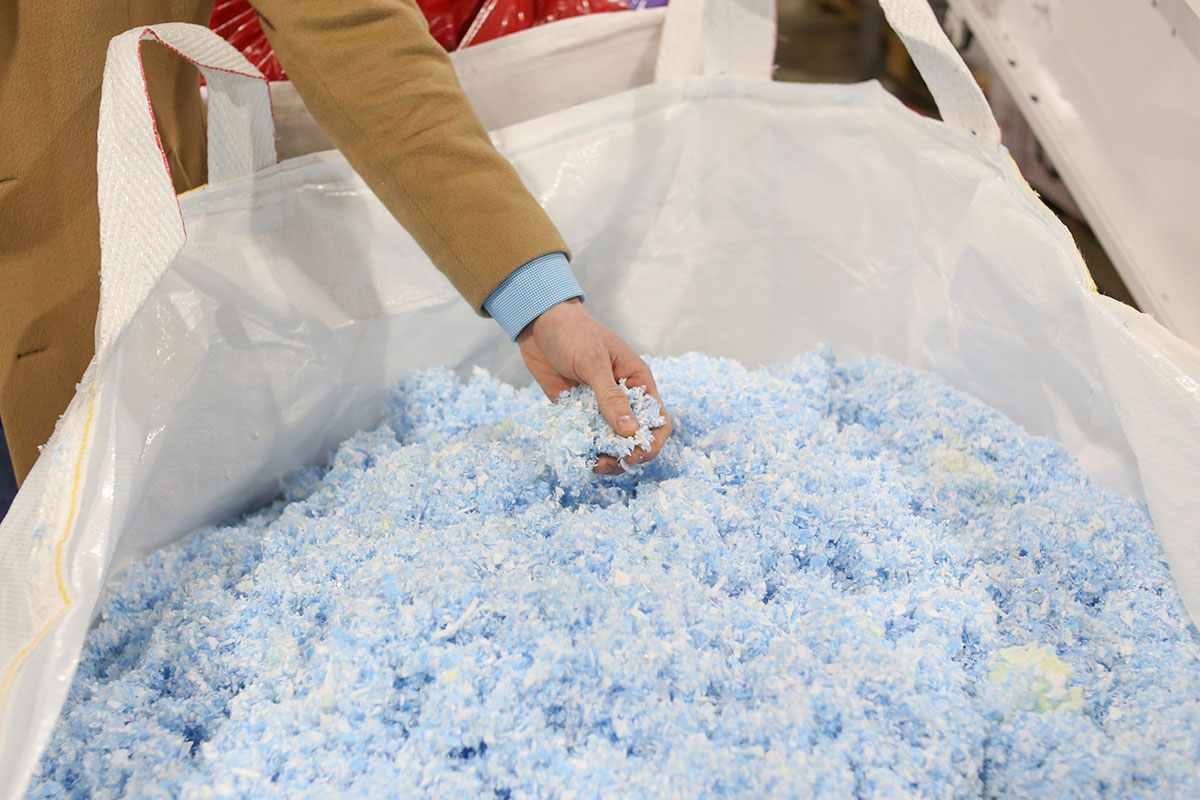
Not every piece of recycled polypropylene goes through the extruder, Moore noted, adding you can stop at extraction to create another polypropylene product that is less “degraded” without heat exposure.
For plastic that does go through the extruder, the “noodles” are cooled in a water bath and dried before being fed down another conveyor belt into a machine that cuts the plastic down into lentil-shaped and -sized pellets.
A shaker drum ensures the pellets are a consistent size before they are filled into a hopper, which drops them into plastic bins, ready to ship to companies that use recycled polypropylene. Most are white, with a sprinkling of brown that indicates even after all that filtering, some other types of plastic are still in the mix.
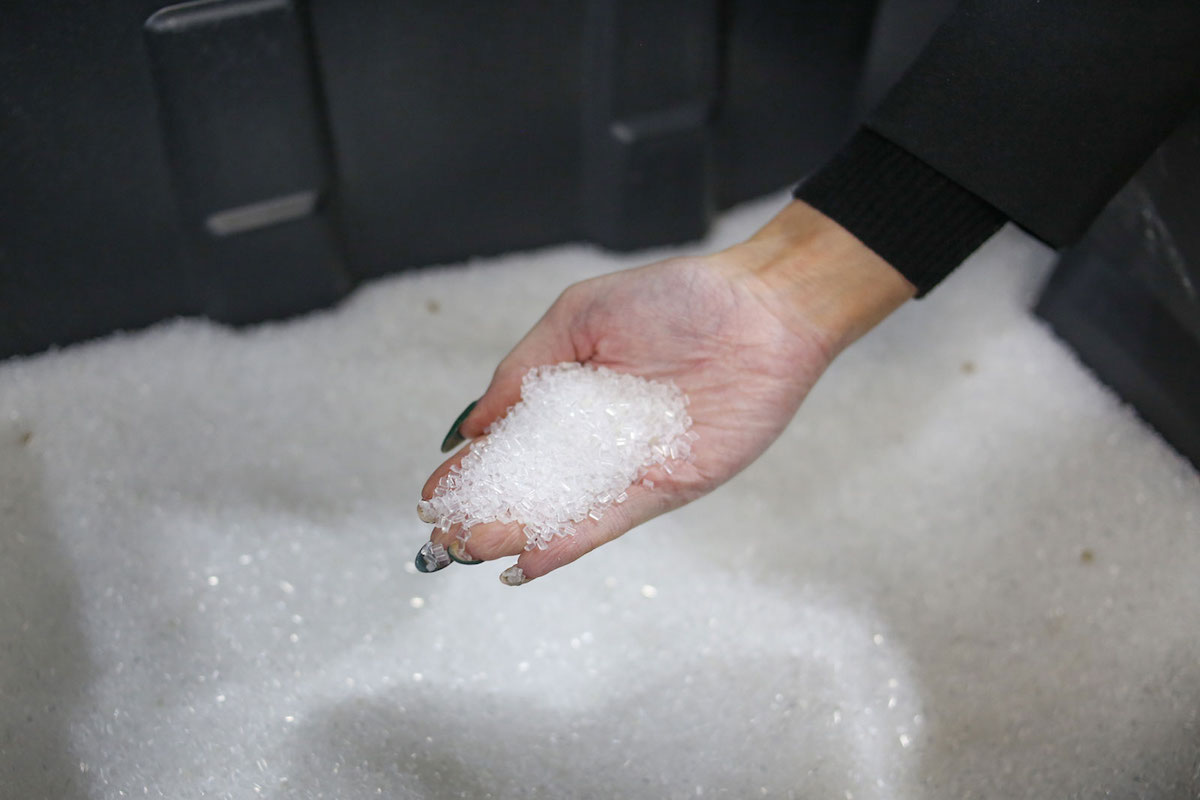
Technically there is no limit on the amount of times polypropylene can be recycled if the heat process is removed or otherwise altered, said Sobkowicz Kline, adding that many of the scientific studies showing a limit to polypropylene recycling do not mimic real-life plastic life cycles.
“There are technologies for recovering that damage, or preventing that damage through additives,” she told The Tyee, adding not every researcher shares her view.
“There are caveats to using additives, but right now when you talk about mechanical recycling, there is no theoretical limit.”
Recycling masks from across Canada
Planet Impact doesn’t just collect and recycle personal protective equipment. Most recently it launched a reusable bag recycling program, partnering with Pattison Food Group last November to put collection bins in its grocery stores. Planet Impact also recycles plastic snack and candy wrappers, plastic packaging and disposable coffee pods.
Vitacore doesn’t currently produce any “second-life” products from the recycled materials, but it sells the materials to other companies that do. Products made from recycled polypropylene can include automobile parts, concrete, storage bins, food containers and medicine bottles.
“We would like to eventually make some products, just to be able to show the life cycle,” Moore said.
But the company’s main goal is to be able to track where the recycled materials end up. So when a customer asks what became of their used masks, Vitacore can say how much recycled material it created, where it went and what products it became.
Planet Impact provides health-care centres and hospitals, industrial work sites, food packing and processing facilities, schools and businesses with PPE collection boxes.
Vitacore currently accepts used and expired personal protective equipment from all 10 provinces, though most of the hospital collection happens in B.C.
“We have a collection facility in Ontario, and so that kind of acts as a depot for us. The goal is to ship as little air across Canada as possible,” Moore said, adding they bale and compress materials at the Ontario facility before shipping them to Port Coquitlam for recycling.
Eventually Vitacore hopes to open another recycling facility in Ontario, but in the meantime this process saves energy and consumer costs.
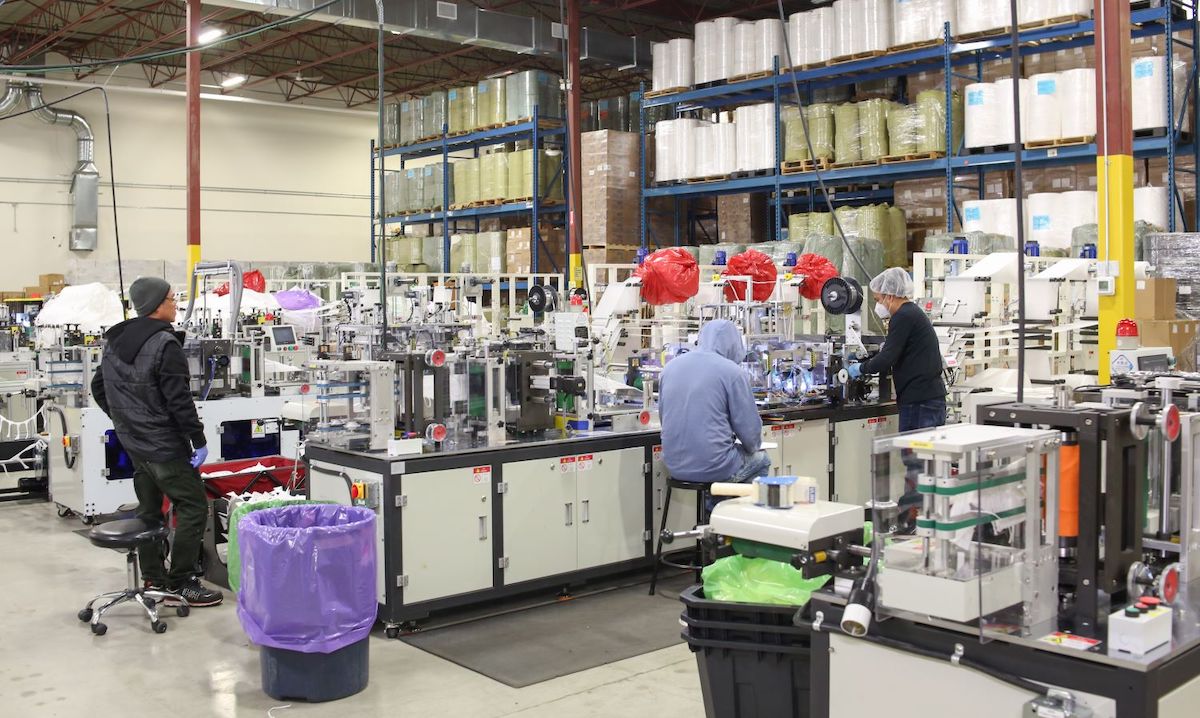
Just under 50 people work at Vitacore Industries Inc. The recycling line takes seven workers to operate, plus an additional two employees as warehouse hands.
Vitacore estimates it has recycled 651,000 kilograms of personal protective equipment since early 2021, equivalent to over 130 million masks.
Circular economy plastic
The road to recycling success hasn’t been a fully smooth one.
In 2022 WorkSafeBC fined Vitacore over $13,000 for workplace safety violations in its mask manufacturing that took place the previous year.
Moore told The Tyee that the company is disputing the fine, saying it was partly due to overreporting minor incidents to WorkSafe, and partly because some of the mask manufacturing equipment imported from other countries was not up to local safety regulations.
Safety upgrades have since been made to the machines to bring them up to Canadian standards, Moore added, and there haven’t been any health and safety incidents since.
While most reporting in the What Works series has focused on the circular economy of the natural world, Vitacore believes a circular economy includes the vital role plastics play in our society.
From oil drilling and extraction to refining, to making monomers, polymerizing them and manufacturing the product, making new plastics requires a lot of energy.
“It’s essentially a solid form of carbon bonds, similar to how gasoline is formed out of carbon bonds,” Moore said.
“And if we throw that into a landfill, we’re basically having to pull up oil again and recreate that entire polymer, releasing all that CO2 again just to make a new product.”
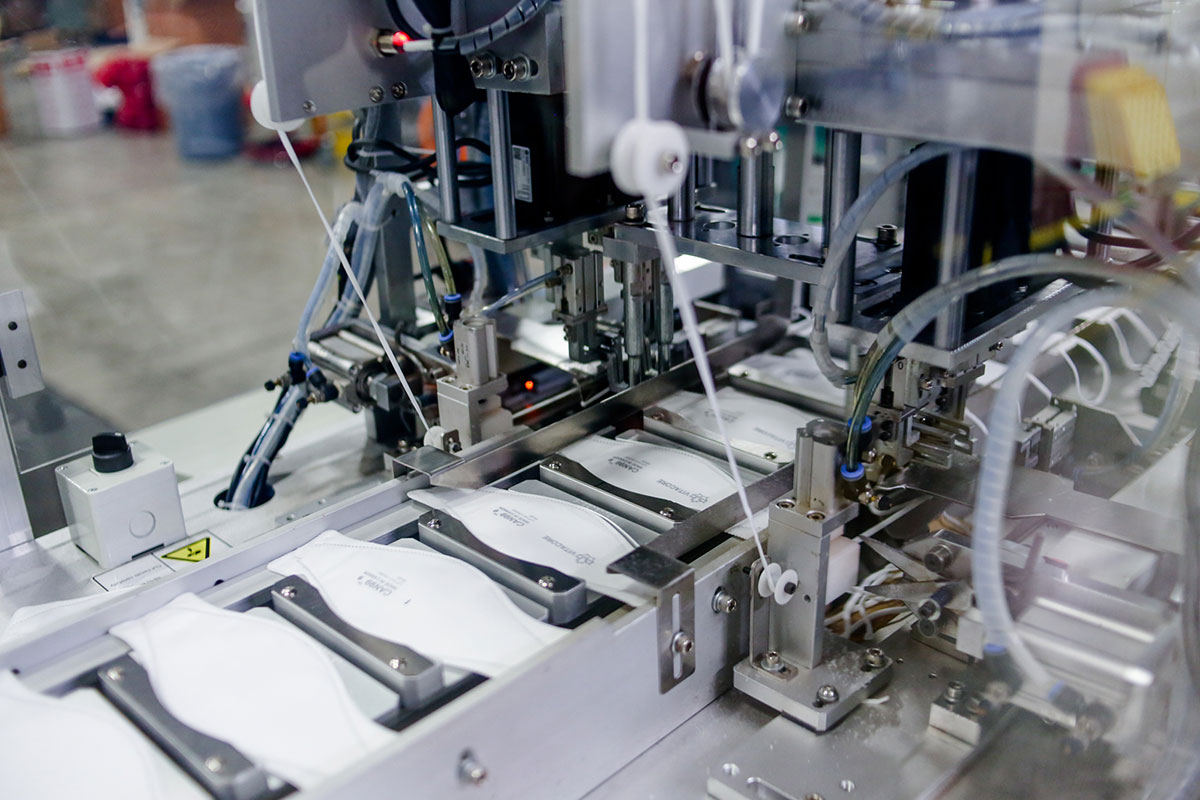
The closest we currently have to “full circular economy” of plastics in Canada and the United States is for polyethylene terephthalate or plastic No. 1, what Sobkowicz Kline refers to as “bottle to bottle” recycling.
“You’re going into the exact same object you came from. Whereas if you recycle into some other application that might have a low value, that’s considered down-cycling,” she said, adding down-cycling is still better than not recycling at all.
“If we can add value to any of those recycled waste streams by having high-value products that we recycle them into, then that’s going to drive that recycling,” Sobkowicz Kline added.
This should be the method for creating plastic products, Moore said. But because Canada invests more in oil extraction and refining than we do in recycling, it is still more cost-effective to create new plastics than it is to make second-life — or third-, fourth- or fifth-life — products.
But as the climate crisis continues to amp up and easily extractable oilfields dry up, Moore predicts an increase in plastics recycling with a downturn in oil production.
We’re already beginning to see the value of recycled polypropylene surpassing that of “virgin” plastic. This is in part due to government legislation and to demand for products made by companies that have committed to using recycled materials.
If companies like Vitacore are successful in expanding their polypropylene recycling to become the norm for health care, manufacturing and other industries, Sobkowicz Kline sees post-consumer polypropylene recycling — tossing it in the blue bin — coming eventually.
“We develop the technologies and the know-how, and then we can spread that across more forms of those waste streams,” she said.
Read more: Health, Local Economy, Environment
Tyee Commenting Guidelines
Comments that violate guidelines risk being deleted, and violations may result in a temporary or permanent user ban. Maintain the spirit of good conversation to stay in the discussion and be patient with moderators. Comments are reviewed regularly but not in real time.
Do:
Do not: